What is Rigging? A Comprehensive Guide to Industrial Rigging
Everything you need to know about industrial rigging and maximizing safety and efficiency in your projects.
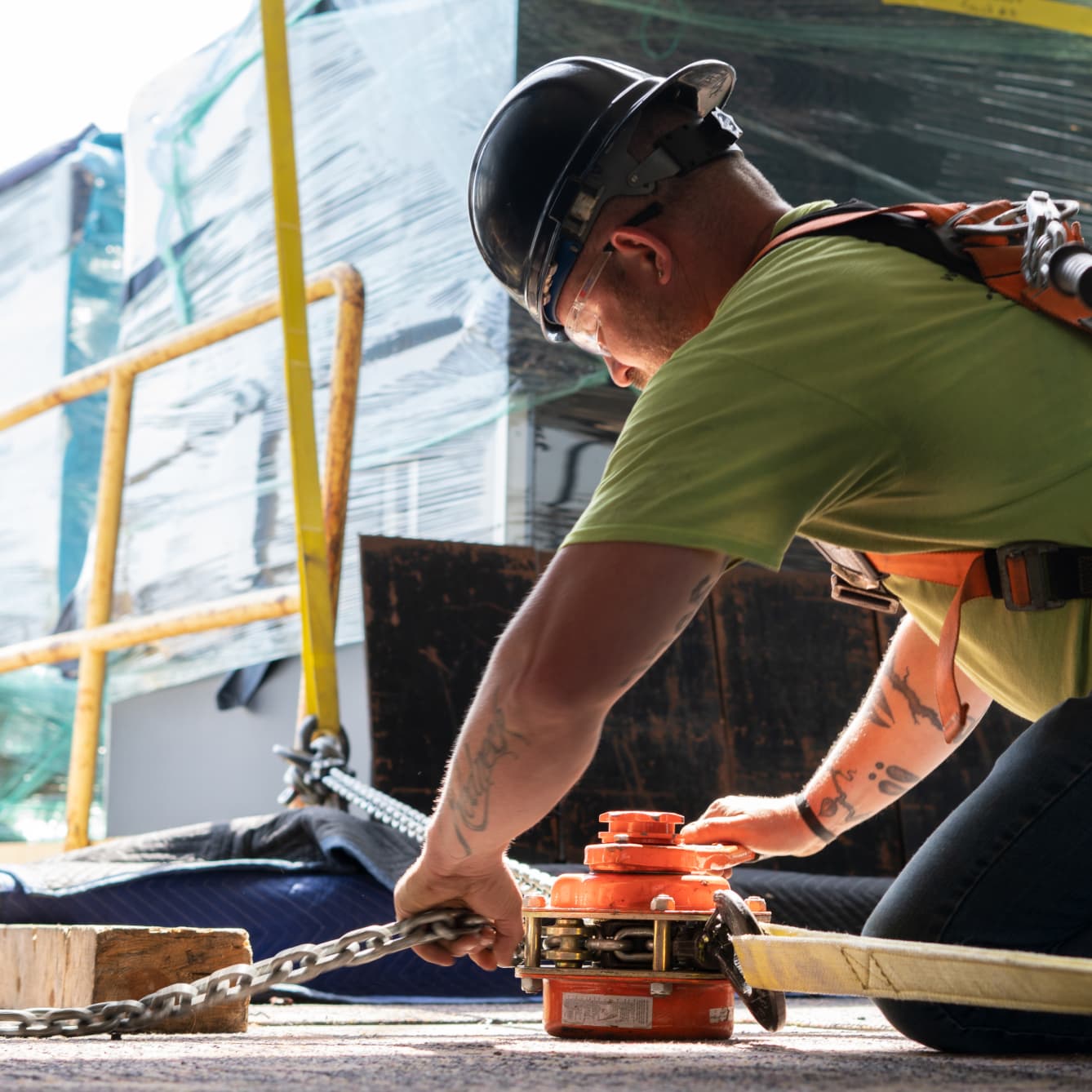
Introduction
We know you're probably thinking, "What is rigging anyway?" Well, it's a term that's used in various industries, but for those in the construction field, it's how we tackle most of our industrial challenges. So, if you're curious about how rigging could be the solution to your problem, check out this guide for all the details. We'll break down what rigging is, how it works, and how it could solve your unique challenge.
Let us shed some light on the world of rigging for you.
Chapter One: What is Rigging?
Rigging (En), Rigge (Nor), Gréement (Fr), Takelwerk (Gr), Rigano (It), Ajustagem (Port), Aparejo (Sp)
rig·ging – noun – circa 1400 Scandinavia - 1. the system of ropes, cables, or chains employed to support a ship's masts and to control or set the yards and sails 2. assemble and adjust the equipment to make it ready for operation.
So you may be wondering how does this ancient Scandinavian term relate to the dynamic world of construction? Well, let's dive deeper into the connection between rigging and the construction industry.
While the tools and equipment used in modern rigging may have advanced from those used in Scandinavia circa 1400, the principles and techniques remain similar. In the realms of construction, industrial operations, and entertainment setups, the term "rigging" holds significant weight. It encompasses the art of setting up and arranging equipment to achieve specific objectives.
Hydraulic jacks, 20-ton forklifts, maneuverable 36-ton steer skates, and sturdy triple-axle tilt trailers stand as indispensable allies in the rigging process. Their capabilities facilitate hoisting, secure fastening, and meticulous balancing of substantial equipment. By leveraging these tools and equipment, rigging professionals ensure that heavy machinery finds its rightful place, firmly anchored, and ready for operation.
The careful orchestration of rigging elements allows for the safe and efficient handling of massive loads. So whether it's installing large machinery or setting complex production lines, the process of rigging is essential in ensuring the seamless execution of these tasks.
Chapter Two: Types of Rigging Equipment
Rigging equipment is a vital part of any heavy lifting or moving process. Different types of rigging equipment are used for different tasks to ensure that the process is carried out safely and efficiently.
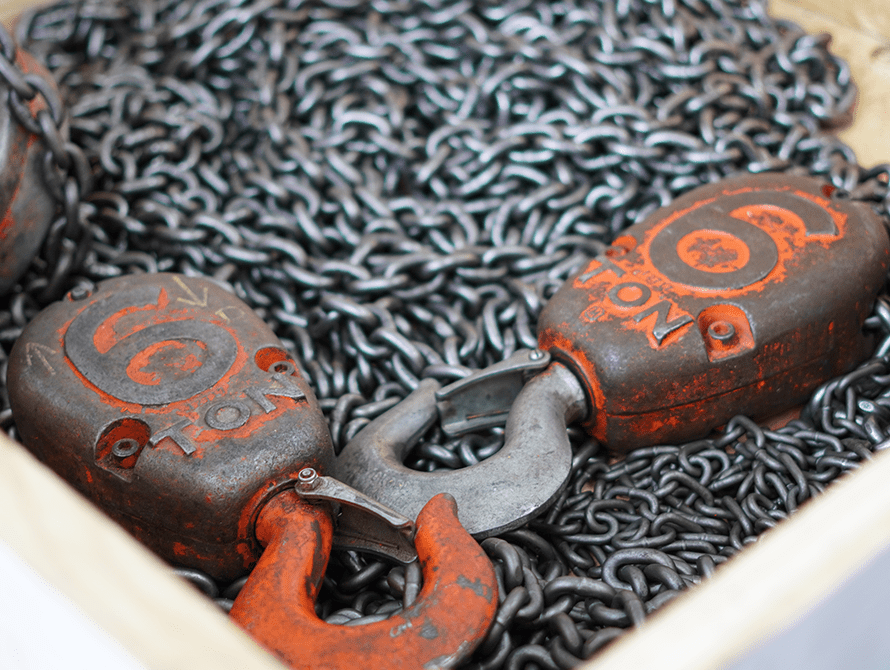
When it comes to rigging jobs, knowing which equipment and when to use it is essential to ensure a smooth and safe operation. For machinery installations where space is limited, a small forklift and skates are essential to getting equipment in place while large generators or air handling units often rely on cranes due to their weight capacities.
A few examples of other rigging equipment include:
- Shackles are used to connect chains, slings, or other lifting devices during the moving or lifting process.
- Chain falls are another type of equipment that helps assist in lifting heavy objects.
- Slings, which are usually made from synthetic material, are a flexible lightweight device utilized for lifting heavy loads. There are two types of slings, endless and eye-to-eye slings.
- Spreader bars or lifting beams are devices that interface the object and the crane while lifting.
- Lifting beams balance out the weight of the load for a more manageable lift while spreader beams distribute the load widely and make it easier to convey.
- Ratchet or hydraulic jacks are used to raise and lower machinery equipment in order to get slings or skates underneath for movement.
- Machine skates are used daily for moving heavy loads with less effort or in tight spaces where it’s too difficult to maneuver forklifts. With weight capacities ranging from 3T to 130T, machine skates are low profile to keep loads close to the ground and have non-marking, non-damaging wheels.
Don’t have time to read this now?
Download a free copy of this comprehensive “What is Rigging” Guide
Chapter Three: Rigging Techniques
Rigging jobs involve the use of various techniques to safely lift and move heavy loads. Different techniques are used depending on the size and weight of the load, the location of the pick, and other factors.
In this section, we will explore different rigging techniques commonly used in the industry. Each technique has its own advantages and is used in different situations to ensure a successful and safe rigging operation.
Crane rigging: Versatile and Precision Rigging for Heavy Load Lifting and Transportation
Crane rigging is a versatile and essential technique employed in various scenarios to lift and transport heavy loads with precision and efficiency. The crane, equipped with an array of specialized components, including cables, hooks, shackles, slings, and counterweights to balance large loads, plays a crucial role in securely fastening the load and facilitating its smooth movement to the desired location. This technique proves particularly valuable when handling rooftop units or large machinery that necessitates overhead picking. Whether it's the installation of air handling units atop high-rise buildings or the relocation of massive industrial equipment, crane rigging ensures the seamless execution of these tasks, minimizing the risk of damage and optimizing operational productivity.
Maintaining Control and Safety: The Significance of Tailing in Heavy Load Operations
When it comes to lifting or lowering heavy loads, tailing plays a crucial role in maintaining control and preventing potentially hazardous situations. By utilizing a tagline, a secondary line attached to the load, riggers can effectively manage the load's movement and minimize the risk of swinging or spinning. This practice is especially essential in crane operations, where the tagline is typically secured to the unit being lifted to ensure consistent control throughout the process. With tailing, riggers can confidently navigate the challenges of load handling, ensuring the safety of both personnel and the surrounding environment.
Chain Hoisting: Effortlessly Lift and Maneuver Heavy Loads in Restricted Spaces
In situations where a crane is not a viable option due to space limitations, the technique of chain hoisting becomes a game-changer. This versatile method involves the use of a chain hoist, which is attached to the load and lifted using a robust chain or cable system. Whether it's a tight corner of a factory floor or a confined construction site, chain hoisting excels at navigating such constrained areas with ease. This makes it an invaluable solution for picking up and setting heavy machinery, facilitating machine moves, and ensuring seamless installations. With the flexibility and precision offered by chain hoisting, even the most challenging lifting tasks can be accomplished efficiently and securely.
Wire Rope Rigging: Securely Lift and Transport Heavy Loads with Ease
When it comes to handling substantial weights, wire rope rigging proves to be an indispensable technique. This method utilizes strong and durable wire ropes that are meticulously fastened to the load, allowing for safe and efficient lifting and movement. Whether it's the loading and unloading of equipment onto trucks or the relocation of hefty objects that surpass the capacity of traditional slings, wire rope rigging gets the job done with precision. By employing a crane or other specialized lifting equipment, the wire ropes enable controlled and reliable hoisting, ensuring the utmost safety and stability throughout the operation. From construction sites to industrial facilities, wire rope rigging stands as a reliable solution for tackling heavy-duty lifting challenges with confidence.
Versatile and Reliable: Harnessing the Power of Sling Rigging for Efficient Load Lifting
Slings are wrapped around the load and then lifted using a crane or other lifting equipment. Typically, nylon slings are used to choke, basket, or pick vertically for any equipment that’s needed to be picked in the air, or it can be used to pick equipment that is awkward and has no flat surfaces to be picked with a forklift.
Jacking and Rolling: Efficient and Secure Load Handling Solutions
This method involves utilizing hydraulic or mechanical jacks to lift heavy loads off the ground or lower them into position with precision. Once lifted, the load is placed on machine skates, allowing for smooth and controlled movement to the desired location.
Unlike forklifts or other large handling equipment, machine skates offer superior maneuverability in confined spaces. They are equipped with low-friction rollers or wheels that allow precise movement in any direction, making it easier to navigate around obstacles and tight corners.
Machine skates provide excellent control over the movement of heavy machinery. Operators can maintain a steady pace, adjust direction easily, and ensure gradual and controlled movement throughout the process. This minimizes the risk of accidents, ensuring the safety of both personnel and equipment.
Secure Connections: Shackling for Safe and Reliable Load Handling
Shackling involves the use of specially designed shackles that are attached to the load, providing a strong and durable link between the rigging equipment and the lifted object. Shackles are engineered to withstand the immense weight of the load, making them essential components in various lifting operations. Whether it's construction projects, industrial installations, or transportation of heavy machinery, shackles provide a crucial point of connection that enables safe and controlled lifting.
Shackles are predominantly used in conjunction with crane work due to their strength and reliability. However, they are also utilized in any overhead picking scenario involving slings. By attaching the shackles directly to the piece being lifted, operators can effectively distribute the load's weight and minimize the risk of slippage or detachment.
Shackles are designed to withstand harsh working conditions, including extreme temperatures, corrosive environments, and heavy-duty applications. Their robust construction and material composition make them resistant to wear, ensuring long-lasting performance even in demanding industrial settings.
Efficient Load Support: Unlocking the Power of Lifting Beams for Safe and Stable Lifting Operations
Lifting beams are ingeniously designed to bear the weight of the load and evenly distribute it along the beam's length. This not only helps in maintaining the structural integrity of the load but also prevents any excessive stress on specific points that could lead to potential damage or deformation. With their robust construction, lifting beams are capable of withstanding significant loads, making them an ideal choice for a wide range of applications.
The versatility of lifting beams is a significant advantage. They can be positioned both over and under the machinery or load being moved, allowing for flexibility in different lifting scenarios. When used overhead, the lifting beam acts as a secure anchor point, providing stability and support to the load during the lift. On the other hand, when positioned underneath the load, the lifting beam ensures that the weight is evenly distributed, minimizing the risk of load imbalances and enhancing lifting safety.
By leveraging efficient load handling techniques, you can ensure the safe transport and delivery of your valuable equipment. Whether it's lifting, securing, transporting, or packaging heavy loads, utilizing reliable methods is key to maintaining operational efficiency and minimizing potential risks.
Chapter Four: The Importance of Rigging Safety
Heavy equipment rigging involves the use of cranes, hoists, slings, and other equipment to lift and move large and heavy loads. While this work can be essential for construction, manufacturing, and other industries, it also poses significant risks and hazards.
Potential Risks and Hazards of Heavy Equipment Rigging
In industries where heavy equipment rigging is a common practice, involving the use of cranes, hoists, slings, and other specialized equipment, it is vital to prioritize safety due to the inherent risks and hazards associated with the work. While rigging plays a crucial role in construction, manufacturing, and other sectors, it can expose workers to significant dangers that require careful attention and precautionary measures.
Crush injuries are a significant hazard in rigging. Workers can be caught between loads and fixed structures or between moving loads and other equipment, leading to severe injuries or fatalities. Additionally, working around power lines or electrical equipment that weren’t properly disconnected pose a risk of electrocution, highlighting the importance of being mindful of electrical hazards in rigging operations.
Another risk in rigging operations is the potential for falls. Workers may find themselves at elevated heights while performing rigging tasks on platforms, scaffolds, or ladders, making them susceptible to severe injuries or even fatalities if they fall. The risk of struck-by accidents is another concern, as workers can be struck by loads that are being lifted, moved, or positioned, resulting in severe injuries or death.
Equipment failure is a significant concern as well. Cranes, hoists, slings, and other rigging equipment can fail due to factors such as overloading or poor maintenance, resulting in loads falling and causing harm to workers. Employing proper rigging techniques and ensuring regular equipment inspections are critical to prevent such incidents.
Improper rigging practices or the use of damaged or defective equipment can lead to loads shifting or falling during lifting or transport, causing injuries or damage. Therefore, it is essential to prioritize proper rigging techniques and ensure the integrity of equipment to minimize the risk of accidents.
Working outdoors exposes rigging personnel to environmental hazards. Extreme weather conditions can pose risks such as heat stroke, hypothermia, or slip-and-fall accidents, emphasizing the need for appropriate precautions and measures to protect workers in such environments.
The physically demanding nature of rigging work can result in fatigue and overexertion, leading to injuries such as strains or sprains. Proper training, scheduling, and adherence to safe work practices can help mitigate these risks.
To address these risks and hazards, it is crucial to prioritize safety. This includes providing workers with comprehensive training on rigging procedures and safety protocols and equipping workers with appropriate personal protective equipment (PPE), such as hard hats, safety glasses, and gloves, to safeguard against potential hazards.
Employers play a vital role in maintaining safety standards by conducting regular safety inspections, ensuring proper equipment maintenance, and promoting safe rigging practices. By identifying and addressing potential hazards, employers can create a safer working environment for rigging personnel.
47.4%
Of workers in transportation and material moving, construction and extraction occupations accounted for fatal occupational injuries according to OSHA.
14,800
OSHA citations were completed in 2022 resulting in $23.9M penalties according to The Center for Construction Research and Training
30
Hour intensive OSHA training course provides employees with the knowledge to recognize, avoid, and prevent common workplace hazards. This isn’t always mandatory but highly encouraged.
Safe Rigging Practices
As we previously mentioned, rigging is an extremely dangerous field and ensuring the safety of employees, customers, and the general public on a jobsite should always be the top priority. Safe rigging practices are essential for minimizing risks and hazards associated with heavy equipment rigging.
Here are some tips that can help ensure safe rigging practices:
- Properly train workers: Workers involved in rigging should be properly trained on safe rigging practices, including how to inspect equipment for damage, how to select the correct rigging equipment and techniques for the load being lifted, and how to work safely around the crane or other lifting equipment.
- Conduct regular equipment inspections: Regular inspections of rigging equipment, including slings, chains, and shackles, can help identify any damage or defects that could compromise the safety of the rigging operation.
- Follow load rating guidelines: The weight and dimensions of the load should be carefully considered, and the rigging equipment used should be rated to handle the load being lifted. Overloading equipment can lead to equipment failure or a load dropping.
- Use the proper rigging equipment: The proper rigging equipment should be used for the load being lifted, such as wire ropes, synthetic slings, or chain slings. The rigging equipment should also be inspected to ensure it is in good condition and properly rated for the load being lifted.
- Use tag lines: Tag lines, which are ropes attached to the load being lifted, can help control the movement of the load during lifting or positioning, reducing the risk of struck-by accidents.
- Communicate effectively: Effective communication is crucial during rigging operations. All workers involved in the operation should understand their roles and responsibilities and communicate effectively with each other to ensure the load is lifted and positioned safely.
- Properly position workers: Workers should be positioned away from the load and the crane's swing radius to reduce the risk of being struck by the load or the crane.
- Perform a site assessment: Before starting a rigging operation, perform a site assessment to identify any hazards such as power lines, uneven ground, or other obstacles that could affect the safety of the operation.
- Use proper PPE: Workers should wear appropriate personal protective equipment (PPE), including hard hats, safety glasses, gloves, and steel-toed boots, to protect against falling loads or other hazards.
By following these tips, employers and workers can help ensure safe rigging practices, reducing the risk of injuries or fatalities during heavy equipment rigging operations.
Let’s Tackle Your Next Rigging Project
Chapter Five: Rigging Training
With the potential hazards involved in rigging projects and their materials, the reliability and competence of trained personnel are vital for safeguarding the well-being of fellow workers, customer property, and the general public.
"Riggers need to be trained on how to evaluate a lift, lift planning, and proper rigging selection for the lift, prior to proceeding."
For the safety of the riggers and the surrounding environment, training on the proper selection and use of rigging is very important. When hoisting loads overhead, there is potential for serious injury, death, or property damage if the piece being rigged shifts, slides, or breaks free from the rigging in which it is suspended from. Riggers need to be trained on how to evaluate a lift, lift planning, and proper rigging selection for the lift, prior to proceeding.
To meet the OSHA qualification requirements to perform rigging on a construction site, at a minimum, employees must go through employer provided training to qualify them as a Competent Rigger. At the conclusion of this training, the rigger will understand proper practices, selection of equipment, lift planning, and inspection of equipment. To become a certified rigger, third party training can be obtained through local union halls or organizations specializing in rigger training such as NCCCO (National Commission for the Certification of Crane Operators).
To perform any rigging on a job site, it is a requirement to be a trained or certified rigger. Knowing and performing proper rigging practices is a valuable company tool for gaining employment and a solid reputation. There are many potential hazards when it comes to rigging of equipment and materials. The safety of the surrounding trade workers, customer property, and public, relies on quality work being performed by trained personnel.
Chapter Six: FAQs about Rigging
Now that you've delved into this informative guide, we understand that you may still have burning questions about the complex topic of rigging. Don't worry, you're not alone! Discover this selection of commonly asked rigging questions that we've received over time.
-
The successful installation of machines depends on several factors, including the accessibility of the site, presence of any barriers within the building that cannot be disconnected or relocated, and the size of the machine itself. In most machine installations, a range of rigging equipment is utilized, such as forklifts, jacks, and skates, to facilitate the process. However, in cases where the available space is extremely tight, pry bars and sheet metal may be employed to navigate through confined areas while minimizing the lifting height of the machine.
To ensure a smooth installation process, it is crucial for customers to prepare the site adequately. This involves marking off the area around the dock or ground door, allowing sufficient space for the machine to enter and maneuver. Additionally, it is essential to disconnect any obstacles that the machine may encounter during the installation, ensuring a clear path for the equipment's seamless integration. By taking these preparatory measures, customers can contribute to the overall efficiency and success of the machine installation process.
-
Effective communication and coordination enable the sharing of crucial safety information and instruction which is vital for any rigging operation. Rigging personnel can communicate hazards, safe work practices, and specific rigging requirements to other job site workers, ensuring everyone is aware of potential risks and follows the necessary safety protocols. This helps prevent accidents, injuries, and damage to equipment or property.
-
The skilled trade shortage has undoubtedly made its impact on the rigging industry, as an increasing number of young adults have traditionally veered towards pursuing college education rather than entering the trades. However, there is a glimmer of hope amidst this challenge. Programs are actively addressing the issue, and with the rising costs of college programs, the skilled trades are becoming increasingly enticing.
In the realm of rigging, where specialized training is a cornerstone and the demand for skilled riggers remains high, this shortage presents a remarkable opportunity for those who choose to embark on a trades program. The field offers competitive pay and a wealth of untapped opportunities waiting to be explored.
For those facing a shortage of skilled labor and lacking the necessary expertise to complete their projects, relying on an external contractor becomes an excellent solution. By doing so, companies not only save on the costs associated with extensive labor and training but also free up their in-house maintenance staff to focus on other critical tasks within the plant. It's a win-win situation that offers both cost savings and logistical relief, ensuring the smooth progress of your project without compromising on quality or efficiency.
Chapter Seven: Conclusion
If you’re looking for a dependable rigging company that delivers exceptional services to fulfill your rigging requirements look no further than Boulter. As a trusted industry leader, we pride ourselves on offering top-notch rigging solutions tailored to your specific needs.
Service from Boulter has always been professional with experienced personnel with appropriate tools/materials, etc "
Our team of experts has extensive experience and knowledge in the rigging industry, enabling us to tackle any project, no matter how complex or challenging it may seem. We use a variety of techniques to ensure that your project is completed safely, efficiently, and on time.
Boulter Tackles the Industry’s Toughest Rigging Challenges
Whether you're tackling a complex industrial project or embarking on a machine move, Boulter is the partner you can rely on. We are dedicated to providing reliable, efficient, and safe rigging services that exceed expectations. Experience the Boulter difference and unlock the potential for seamless and successful rigging operations.
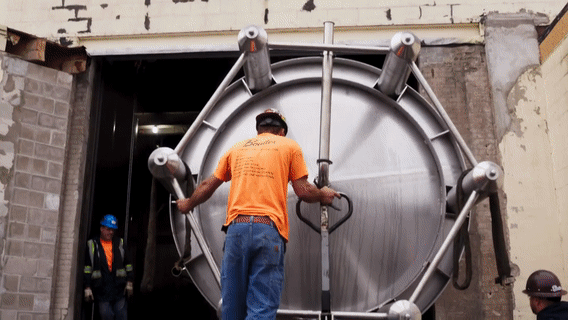
Ready to Start Your Rigging Project? Schedule a Call with Our Experts!
Now that you have gained a solid understanding of rigging fundamentals, you may be eager to kickstart your project with the help of a rigging expert. We are here to provide you with valuable insights and guidance tailored to your specific rigging needs.
- Discuss your unique project needs with a rigging expert
- Receive valuable insights to help your project succeed
- Save time and resources