Manufacturers Understand There's Nothing More Frustrating and Expensive than Unplanned Downtime
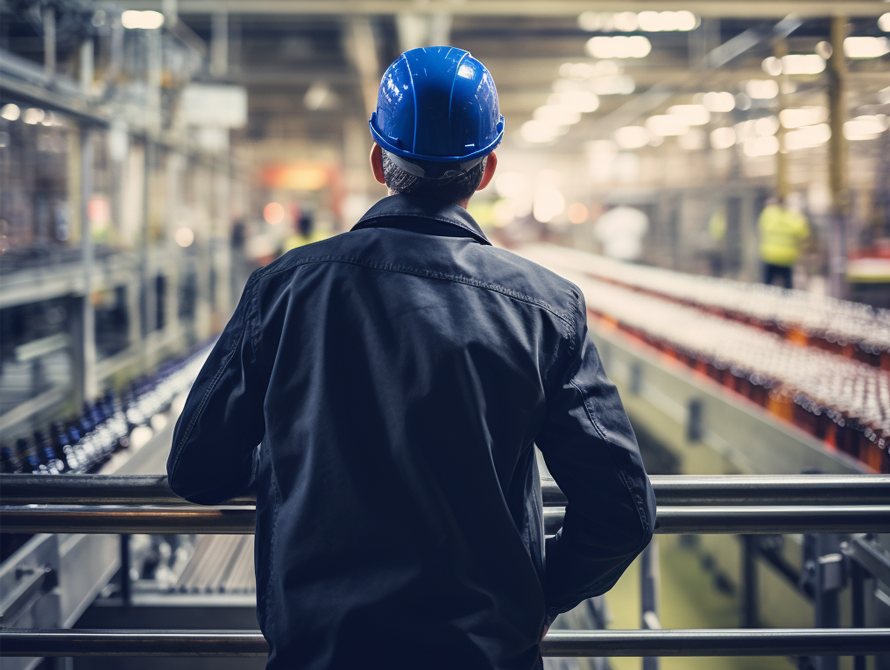
To grasp how to accurately quantify the cost of downtime, it's crucial to delve into a few key calculations: hours of downtime, the average production rate, the number of units not produced due to downtime, and the resultant total gross losses.
Planned Operating Time vs. Actual Operating Time
In manufacturing, a scheduled period of operation, known as planned operating time, is set each day to maintain an efficient production line. Despite these plans, the reality often diverges from the ideal due to factors like equipment failure and human errors. This disparity between the plan and the reality is calculated as "Hours of Downtime."
The Impact on Production Rate
To assess how efficiently a manufacturer is operating, the Average Production Rate per Hour is calculated. To do this, the total number of units produced in a day is divided by the planned operating time. This rate reveals how many units they can produce in an ideal hour of operation.
Unwanted Losses
Downtime carries direct implications for production. By multiplying the total hours of downtime by the Average Production Rate per Hour, we arrive at the number of units that could not be manufactured due to these interruptions. These unproduced units are referred to as 'Units Not Produced.'
Counting the Cost
To comprehend the financial ramifications of these unproduced units, the manufacturer incorporates the Gross Profit per Unit, signifying the earnings from each unit sold. When the number of Units Not Produced is multiplied by the Gross Profit per Unit, the manufacturer quantifies the 'Total Gross Losses.' This figure underlines the imperative for streamlined operations to reduce downtime and enhance profitability.
Speak With Our Maintenance Expert
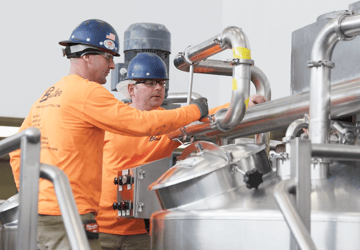
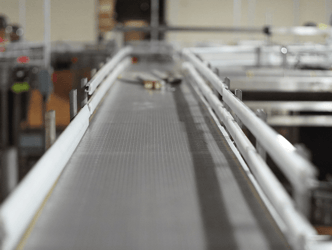