Why Skilled Trades Deserve a Seat at the Innovation Table

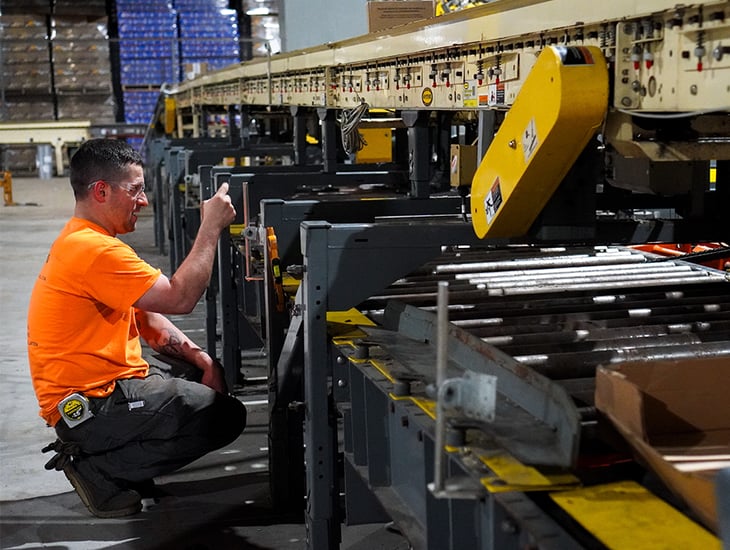
By 2030, an estimated 2.1 million skilled trade jobs in the U.S. will go unfilled. And that’s not just a workforce issue; it’s an innovation issue.
Too often, innovation is seen as the domain of engineers, software developers, and R&D teams. The conversations happen in conference rooms and on whiteboards. But real innovation? It’s also happening 30 feet in the air during a complex rigging lift. It’s happening on the floor of a food plant where a millwright adjusts a system to prevent hours of downtime. It’s happening behind welding masks, in crating shops, and on the back of a forklift.
As advanced manufacturing evolves, skilled trades aren’t just supporting progress; they’re enabling it. So why are they still missing from the innovation table?
The Innovation Conversation Is Too Narrow
When most people talk about innovation, they picture software developers, engineers, or R&D teams in offices sketching the next big idea. And while those roles are absolutely part of the story, they’re only one piece. What’s often missing from the conversation is the role of the people who physically make innovation possible; the ones who install the equipment, troubleshoot the systems, and keep production running when plans hit real-world challenges.
The reality is that a groundbreaking idea means nothing if it can’t be executed efficiently and safely on the floor. The problem is that most companies separate innovation from execution as if they exist in different worlds. But the best operations understand that execution is innovation. When you leave tradespeople out of the equation, you’re not just overlooking labor; you’re overlooking insight, creativity, and experience that can directly impact efficiency, safety, and long-term success.
What Skilled Trades Actually Bring to the Table
Skilled trades bring a level of real-world problem-solving that often goes unrecognized. When a production line breaks down or an install hits an unexpected snag, it’s the millwrights and technicians who step in, assess the issue, and make fast, informed decisions under pressure.
Their work isn’t just physical; it’s precise, technical, and often highly creative. They are on-the-fly problem solvers, maneuvering 30,000-pound presses into place with just inches to spare or welding a structure that must withstand constant vibration and heat. Tradespeople use hands-on ingenuity every day. They also bring something many innovation teams lack: deep institutional knowledge. These are the people who’ve spent years working with machinery, systems, and workflows. They know what breaks, what clogs, what overheats, and more importantly, how to fix it.
And despite the outdated perception that trades are “old school,” most tradespeople are constantly learning. With new technology, updated safety regulations, and evolving client needs, this workforce is quietly adapting and improving in step with the industry, if not ahead of it.
The Consequences of Leaving Trades Out
The disconnect doesn’t start on the job site; it starts in the classroom. For far too long, students have been taught to view college and white-collar careers as the path to innovation, while skilled trades are framed as a fallback. That false narrative undermines not just the trades but the entire economy. Both paths serve an equally important role in driving progress. Engineers design the machines. Tradespeople build, move, and maintain them. One can’t exist without the other.
When we exclude trades from the innovation conversation, we limit our potential. We ignore the problem-solvers on the ground who are constantly adapting, improving, and delivering results in real-time. Culturally, we send the wrong message to the next generation that only those with college degrees can be innovators. If we want to close the talent gap, we need to give tradespeople the recognition and the seat at the table that they’ve earned.
What Inclusion Looks Like
True inclusion means acknowledging that innovation happens in the field just as much as it does in a conference room. For example, when a team is tasked with rigging oversized equipment into a space that was never designed for it, they aren’t just lifting and moving, they’re engineering solutions in real-time. When a crating specialist designs a custom skid to protect sensitive equipment headed overseas, they're solving a logistical challenge that directly impacts the customer’s bottom line.
But inclusion isn’t just about better job sites. It’s about changing the perception of these careers altogether, and that work starts much earlier. Too often, students are taught there's only one “right” path after high school, and it usually involves a four-year degree. That narrative is limiting and outdated. Career and Technical Education (CTE) programs are helping to rewrite the script, showing students other options that lead to real skills, good pay, and long-term success. Programs like SkillsUSA take it even further, offering friendly, high-stakes competition that lets students showcase their abilities in welding, carpentry, electrical, and more. These events build confidence and shine a spotlight on the value of trades-based education.
TV shows like Dirty Jobs with Mike Rowe have also helped push this message forward. He didn’t glamorize the work; he showed it for what it was. Tough, hands-on, and essential. His episodes highlighted the people doing the hard jobs behind the scenes, the ones who keep the world running. That kind of visibility matters. It sends the message that trades are not second-tier, they’re foundational for the economy.
And as we rush toward automation and AI, we need to be honest. You can’t replace hands-on experience with an algorithm. A robot can’t troubleshoot an overloaded conveyor system mid-shift. AI doesn’t know how to disassemble a press that’s jammed under a mezzanine with two inches of clearance. These jobs require instinct, experience, and creativity. You can’t replicate that with software.
Inclusion means showing up for the next generation, creating opportunities, and building awareness about what these careers offer. It means investing in apprenticeship programs, championing workforce development, and working with partners who understand that trades are not just support—they are strategic.
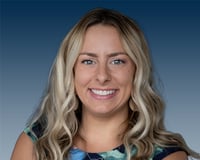
Brittany joined the Boulter team in 2017, following her experiences in the entertainment and healthcare sectors. In her role as Marketing Manager, she oversees all aspects of Boulter's brand management and digital marketing initiatives. However, her passion extends beyond these responsibilities. Brittany is an advocate for encouraging younger generations to explore rewarding career opportunities in the trades, addressing the critical issue of labor shortage.